Part 2: What we will do for brewery designing?
2.1 Brewhouse: Highly matched with your brewing request.
Brewhouse part is the most important part in whole brewery, which is directly related with the wort and beer quality. Brewhouse design must follow exactly your brewing recipe, eg the average beer gravity/plato. Make sure the Mash or lautering process can be finished in reasonable time.
Just as sample of 10BBL brewery system.
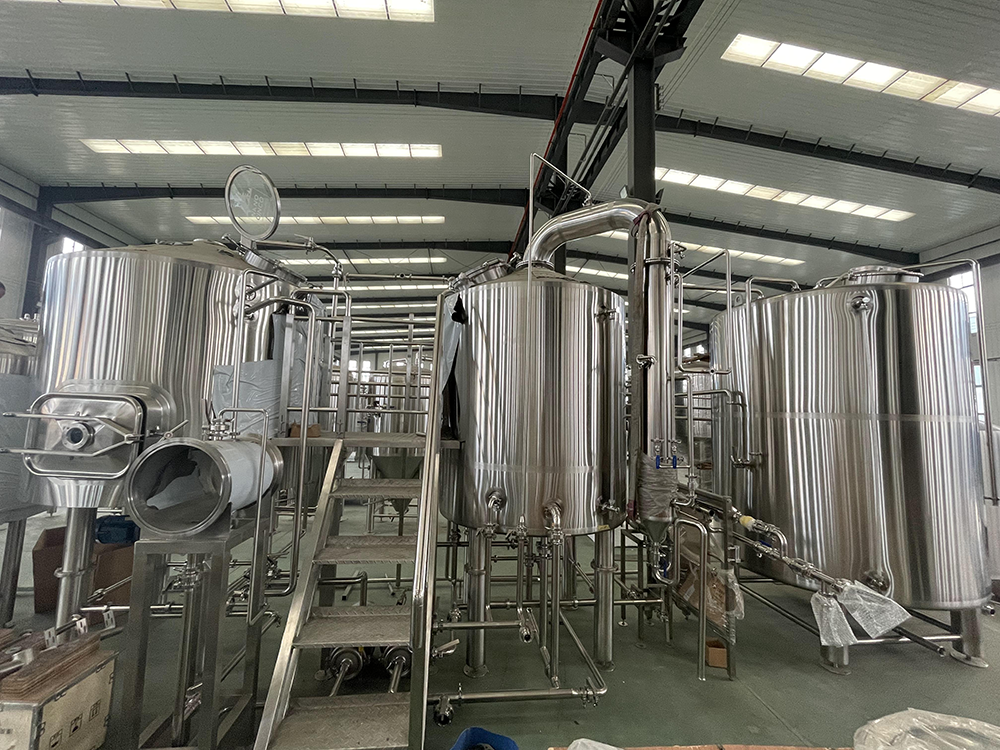
Lauter tank: The diameter of lauter tank is 1400mm, when the wort is 13.5 degrees, the malt feeding amount is 220KG, the equipment using efficiency is for 75%, and the thickness of the grain layer is 290mm; the filtering area is 1.54m2, and the filtering speed is 0.4m/s; The opening rate of the filter sieve is 12%, and there are 6 wort channels on lauter tank.
With the support of these parameters, it is ensured that the filtration time is completed within 1.5 hours, also can make sure you can get clear wort.
When the wort is 16 plato, the feeding amount is 260KG, the tank volume using for 80%, and grain bed thickness is 340mm. That’s to ensure the thickness of the filter layer meets the brewing requirements, does not affect the filtration speed and ensures the production efficiency. Final to improves the output per unit time through reduces the filtration time.
Boiling kettle: The kettle volume design is based on the 1360L wort befor boiling, and the using volume is 65%. Because of the wort concetration is relative higher in abroad, the form will much abundant when boiling. In order to prevent foam overflowing from the kettle during the boiling process, we use the forced circulation function to improve the evaporation rate to ensure the evaporation rate is 8-10% and improve the boiling intensity. A forced circulation with kettle helps increase the evaporation, and the DMS situation and the content within 30PPM, it will reducing the heat loading and ensuring the stability of the wort chroma and avoiding the wort Maillard reaction.
2.2 Lower energy consumption in brewery
Condensor system: The boiling kettle adopt steam condensation recovery system, it will helps to improve the water recovery and save the water and electric consumption in whole brewery. The recovery hot water temperature around 85℃, and hot water recovery capacity at 150L for each batch; That’s means it will save the electic 18kw per batch of the water temperature from 25-85℃.
Wort cooler: The wort heat exchanger area calculate by the brewing process and finish the cooling process in 30-40 minutes, and hot water temperature at 85℃ after heax exchange, heat exchange efficiency of more than 95%. Therefor, we will ensure the maximum energy recovery and lower production costs.
2.3 Easy brewing and reducing maintaining in brewing process
2.3.1 A double strainer configured, in case the client brewing too hoppy beer. So we bring good guarantee on plate heat exchanger, which is the hardest part for cleaning.
2.3.2 The dual pump is necessary for glycol unit, for good guarantee when there is any maintaining request, each pump can be switch easily for keeping the production ongoing.
2.3.3 Dual chiller configured, with the same purpose like glycol pump.
2.3.4 Glycol pump used constant pressure pump and keep the same pressure in whole glycol pipelines, protect the soleniod valve and expanding the using life.
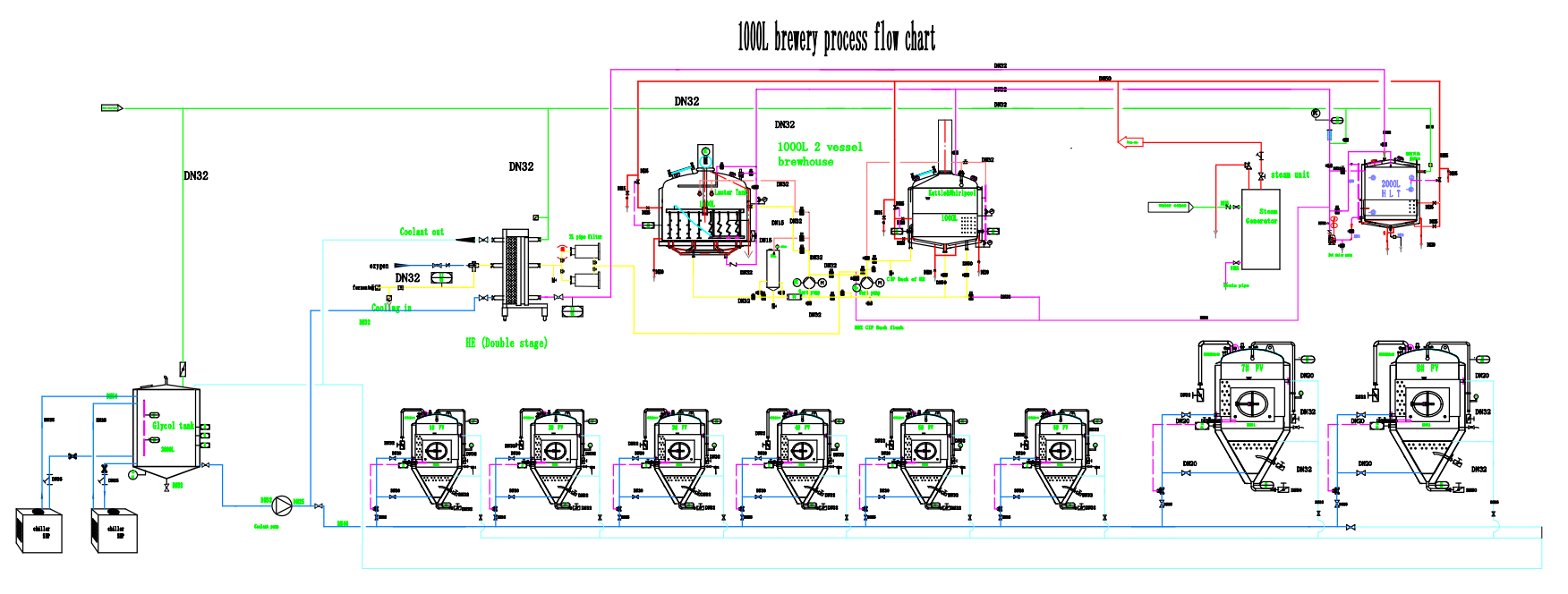
All these details is for the more stable work in whole brewery ruuning, and bring you a good experience in the brewing process.
Post time: Sep-25-2023